The silk road to Lyon
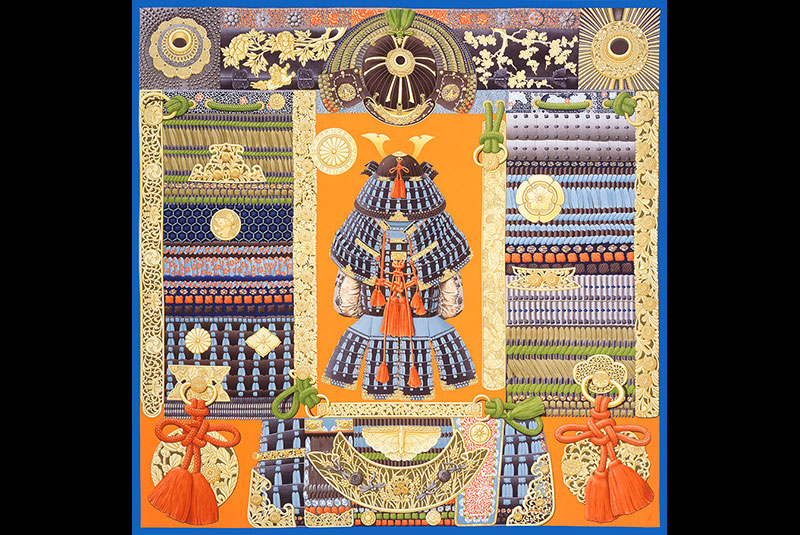
Forty-two colors, meaning 42 screens, were used to print the very intricate details of Parures de Samourai, If the average scarf takes two years from artwork to actual product, this scarf took three years! (Photo from Studio de Fleurs)
Behind the luxe Hermès name stands a very solid philosophy of uncompromising quality. A visit to the facilities of Holding Textile Hermès (HTH) in Lyon was a privilege, allowing us to witness the numerous, meticulous steps in the production of its iconic silk scarf.
Lyon is the historical capital of the French silk industry. Today in Lyon, only Hermès uses the traditional Lyonnaise (serigraphy) method, with artisans of passionate and dedicated discipline working lovingly to produce every piece.
Raw silk thread comes from Brazil, from the Bombyx Mori butterflies whose cocoons must be of exactly the same size. White silk “hair” of the highest quality is put together in a flotte (skeins of raw silk), which are then shipped to Lyon. From this point forward, only HTH handles the production process until the finished products are delivered to Paris for distribution.
How many hairs make up a single thread to be woven into the silk cloth? That’s a trade secret. While the designs to be used are decided upon in Paris, production is actually a refined science executed by the combined eyes, hands and hearts of the Hermès artisans in Lyon.
Under the leadership of Pierre-Alexis Dumas, artistic director of Hermès, designs for scarves are selected from works of different artists. Dumas is the great grandson of Emile Hermès and represents the sixth generation of the family. With him and Bali Barret, Women’s Universe creative director, are engravers, colorists, printers, seamstresses — all expertly skilled in their fields.
The artwork itself is never altered, paying utmost respect to the artist, but the colors are carefully selected to suit the ambiences (color schemes) defined for the spring/summer and fall/winter seasons. Colorists select from a library of 75,000 colors and present different color palettes for approval.
A scarf’s design initially goes into an engraving process that defines each color, complete with all its gradations. This could require an average of 30 colors or more, applied on the silk cloth with screens. The number of colors equals the number of screens.
The scarves are laid out and glued on a 150-meter-long printing bed, where screens apply each color to 150 scarves at a time. Even more processes follow: fixing the colors by steam cooking at 106 degrees Celsius for an hour; washing, drying, cutting; and hem rolling.
These silk pieces are finished by hand — all by hand. These admirable ladies, with their skillful fingers, finish each scarf with a rolled hem — the roulotte — using a matching silk thread and rolling the ends of the slippery silk fabric from back to front, paying strict attention to the corners. One skilled artisan finishes a scarf in 45 minutes, but she has been working in the atelier for over 20 years.
A group of trusted staff, with the sharpest eyes and the most sensitive hands, oversees quality control for no less than100 percent of production. The tiniest dot caused by a dust on the screen, the smallest deviation from the perfect square (the name “carré” stubbornly insists that it be so), or an error in the stitching causes the piece to be rejected. There are no compromises here, no second best. Only the flawless scarves are shipped out to Paris, and, from there, to boutiques worldwide.
But not before each item goes through a metal detector, in case a wayward pin, which could hurt a customer, is hiding somewhere.
An Hermès scarf takes a minimum of two years from the execution of the artwork to the finishing. It requires continuous coordination among the people of every department to do this, since each step depends on the step that came before it — much like a symphony being performed.
Every time you allow an Hermès scarf to caress your neck, please remember that creativity, time, skill, passion and dedication made it possible, this silken gem of “utility and elegance.”
* * *
In the Philippines, Hermès scarves are exclusively available at the Hermès store in Greenbelt 3, Ayala Center, Makati.
Tell me where to Walk the Talk: cecilialicauco2@gmail.com.
Follow me on Instagram: cecilialicauco2.
Threads Of History
• In 1837, the first “customer” of Thierry Hermès, a harness maker, was a horse. The company celebrates its 180th year and 80 years of the silk scarf (1937).
• The logo of Hermès came from a lithograph by Alfred de Dreux and was originally meant for the bookplates in Emile’s library. It shows a sporting carriage generally used by women, with its faithful groom ready and waiting.
I was told that the carriage is empty, because the customer drives the carriage. Case in point: in 1948, neckties were produced because customers of their boutique in Cannes needed these to enter the casinos. Hermès listens to its customers.
• The equation: (1 moth = 300 eggs) + (2 mulberry trees = 300,000 cocoons) = 450,000 meters of silk thread = 1 carré. Simply put: 1 silk moth = 1 carré.
(From “Carrés Behind the Scenes”)
• Hèrmes uses 40 basic colors, has 75,000 colors in its library, and millions of color possibilities.
• Kamel Hamadou, communications manager of Holding Textile Hermès, exudes a contagious passion, treating everyone in the ateliers with fondness. After 30 years, he still wakes up every morning, eager to go to work for Hermès. He says there are very few people who leave the company — this speaks so well of the owners.