Anatomy of an expensive toilet soap bar
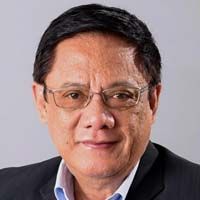
One basic rule in quality and productivity improvement is that management must listen to all employee ideas, even those that appear absurd at first glance.
Try it once or twice. If an absurd idea solves a problem, then it’s not absurd. It’s as simple as that. This came to me again when I talked to a production manager of a Filipino-owned factory in Laguna.
Believe it or not! They were struggling with how to solve the “high cost” of providing regular-size bar soaps for its ten toilets.
The average cost is $2,500 per year. It may not be a costly item to some people, but for this factory, it’s a big deal when they’re high in their kaizen program.
The soaps are being supplied by a cooperative owned and managed by the workers’ parents and spouses as part of the factory’s community relations program.
The kaizen manager thinks it’s too much to spend that much and vowed to solve it as part of their mandate to eliminate all types of waste – big or small. However, department managers are divided on how to solve the issue. They claimed that whatever the cost favors the cooperative as it ultimately benefits its members – all employees and their families.
The kaizen manager and other managers rejected the argument. They claimed that whatever benefit that goes to the cooperative should not result in giving undue disadvantage to the factory. “Fair is fair,” they chorused.
The security manager chimed in. He suspected the workers were bringing home the soaps for family use to stimulate artificial consumption. However, he offered no evidence. Instead, he suggested frisking all workers when they clock out for work even if it appears cumbersome for the guards to monitor more than 1,000 workers, agency workers and subcontractors.
The security manager’s solution was worse. It tends to create another problem. The frisking would also delay the exit of the workers relying on the factory’s seven shuttle service units that must leave the factory premises at exactly 4:15 pm or they risk themselves battling hours of traffic in different intersections.
Industrial democracy
The kaizen manager objected to the frisking as it’s against their “Respect for People” policy - an important component of their kaizen program. Also, it would result in 15 unproductive minutes daily for the workers to line up at the gate if the workers are allowed to stop working at 3:45 pm so they could line up at the biometrics machine and catch the shuttle service in time.
Incidentally, “Respect for People” is an interpretation of the age-old principle called industrial democracy where the workers are empowered to solve problems, decide on certain things and put them fully responsible for their ideas, with limited management intervention.
We don’t use the term industrial democracy every day for fear of alienating the toxic managers in their man cave.
Going back to the issue of the bar soap. A supervisor suggested replacing it with liquid soaps, unmindful that it is also susceptible to pilferage. Imagine people using the ubiquitous empty water bottles as a trade tool for pilferers or their aluminum water bottles. This is not to mention it’s more expensive to make liquid soaps than the bar soaps.
The cooperative relies much on the scrap materials from the factory in making the bar soaps with an average size of three inches by four inches at one-and-a-half inches thick.
Low-cost solutions
The factory has more than six months of inventory of the bar soaps. Therefore, it’s not easy to dispose of them. So, what’s the best, low-cost solution – an important component of kaizen? (If you’ll spend money on the solution, then that’s not kaizen). The kaizen manager tasked the employees to think of the best solution.
They believe that if you trust the workers, they’ll reciprocate for the common good. The workers know and understand their work better than anyone. That’s why we should value their ideas more than anything. They must be trusted so they can do a better job which leads to better operational efficiency. Four workers suggested the following:
Anthony thought of helping the cooperative to market and sell the bar soaps to other consumers outside of the community to reduce the inventory. But who will do the selling? This is also counterproductive.
Bobby proposed they cut the soap bar into six pieces, approximating the size of motel bar soaps. He thought using a scrap of thin wire fashioned out of a saw-like wooden instrument would do the trick. That way, they become unattractive to pilferers.
Charlie opined changing the soap’s formulation so that it becomes unattractive for home use. They could “recook” the inventory with an added ingredient. The question is – would that require additional expenses?
Danny suggested chopping the soap bars into irregular shapes and putting them in scrap plastic nets (used for onion packaging) for hanging on the faucet’s neck. It may look absurd, but it can solve a problem.
What do you think? What’s your low-cost solution? The lesson is clear. If you want to solve big or small problems, you have to seek the help of an army of problem solvers and expect to receive one percent improvement per person. Or, is this problem worth everyone’s time? Of course, when it’s part of a learning experience.
Not everyone can be as bright as Albert Einstein but you can be the best kaizen person anytime you want it.
Rey Elbo is a quality and productivity improvement enthusiast. For free consultations, email your concerns to [email protected] or via https://reyelbo.com. Anonymity is guaranteed.
- Latest
- Trending